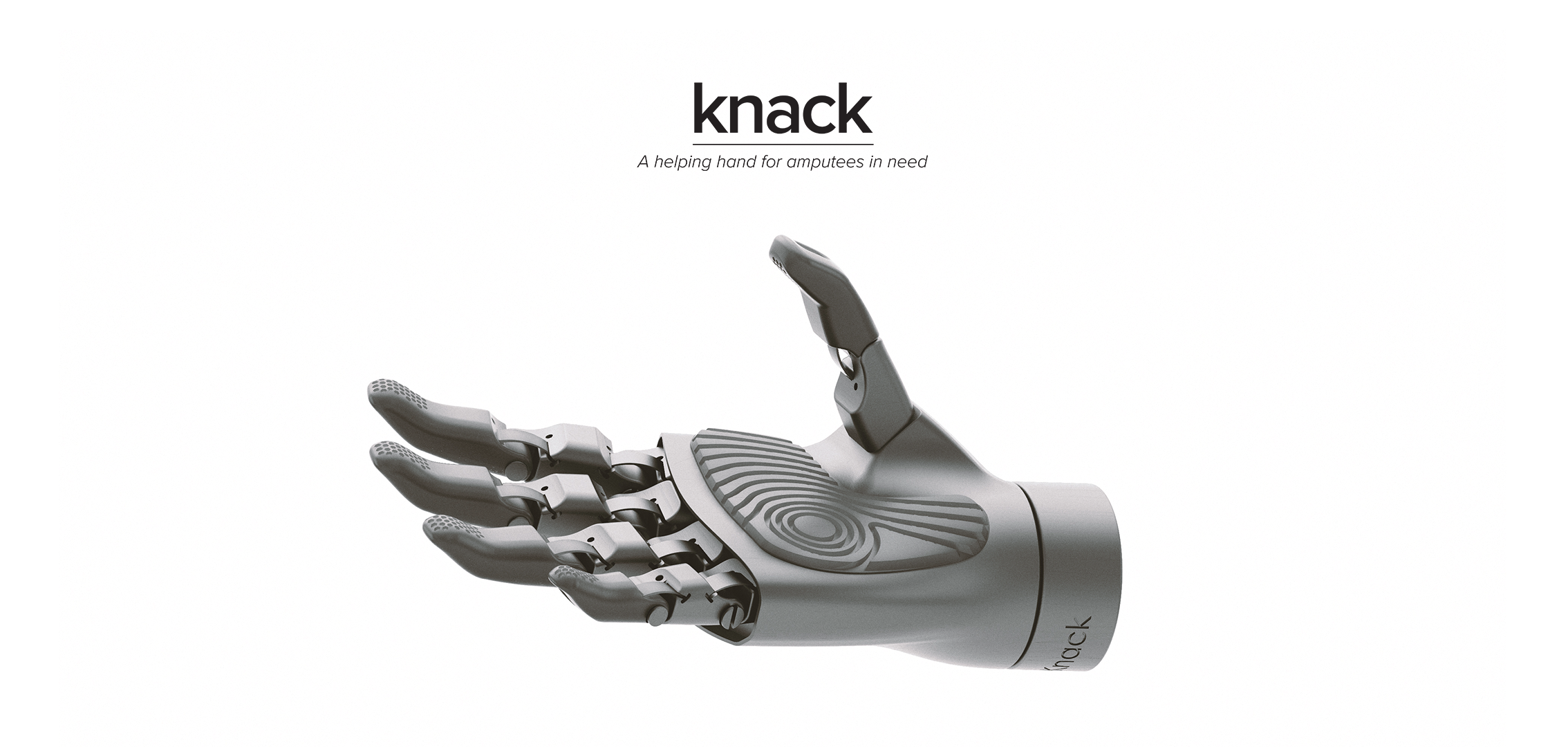
Using just 24 parts, Knack’s modular design makes assembly and modification easy. The unique, compact thermoplastic polyurethane (TPU) springs allow for finger extension without the aid of elastic bands.
Knack was developed through an iterative 3D printed prototyping process. The final prototype was printed using Onyx, a nylon-carbon fiber composite, for rigid surfaces. Touch surfaces, including fingertips, were printed from TPU, for realistic compliance and gripping ability.
Testing was conducted under the guidance of occupational therapists Kay Brown, OTR, CHT, PhD, and Nico Carrizales, OTR. Knack was fitted to a real amputee, using a prosthetic arm unit with an actuator located in the forearm.
The prototyping process involved the creation of many 3D printed models, especially to refine the form and function of Knack’s fingers.
As the most critical component, the design process began with a single finger. The hybrid TPU/PLA construction makes the fingers strong yet compliant, while sturdy snap joints simplify assembly. Innovative TPU springs provide generous return force in a compact form.
A helping hand for amputees in need
Niell Gorman
Niell Gorman is a visual thinker striving to leverage empathetic, human-centered design methods to create impactful, health-focused products and experiences.